Вирощування довгокристалічної печі з карбідом кремнію методом PVT для вирощування кристалічних злитків SiC 6/8/12 дюймів дюймів
Принцип роботи:
1. Завантаження сировини: порошок (або блок) SiC високої чистоти, розміщений на дні графітового тигля (зона високої температури).
2. Вакуумне/інертне середовище: вакуумувати камеру печі (<10⁻³ мбар) або пропускати інертний газ (Ar).
3. Високотемпературна сублімація: нагрівання резистивним струмом до 2000~2500℃, розкладання SiC на Si, Si₂C, SiC₂ та інші газофазні компоненти.
4. Передача у газовій фазі: градієнт температури призводить до дифузії матеріалу в газовій фазі до області низьких температур (зародкового кінця).
5. Ріст кристалів: Газова фаза перекристалізується на поверхні зародкового кристала та росте у напрямку вздовж осі C або осі A.
Ключові параметри:
1. Градієнт температури: 20~50℃/см (контроль швидкості росту та щільності дефектів).
2. Тиск: 1~100 мбар (низький тиск для зменшення потрапляння домішок).
3. Швидкість росту: 0,1~1 мм/год (впливає на якість кристалів та ефективність виробництва).
Основні характеристики:
(1) Якість кристалів
Низька щільність дефектів: щільність мікротрубочок <1 см⁻², щільність дислокацій 10³~10⁴ см⁻² (завдяки оптимізації зародка та контролю процесу).
Контроль полікристалічного типу: можна вирощувати 4H-SiC (основний потік), 6H-SiC, частку 4H-SiC >90% (необхідно точно контролювати градієнт температури та стехіометричне співвідношення газової фази).
(2) Продуктивність обладнання
Стабільність до високих температур: температура графітового нагрівального елемента >2500℃, корпус печі має багатошарову ізоляційну конструкцію (наприклад, графітовий фетр + водяна оболонка).
Контроль однорідності: осьові/радіальні коливання температури ±5 °C забезпечують стабільність діаметра кристала (відхилення товщини підкладки 6 дюймів <5%).
Ступінь автоматизації: інтегрована система керування PLC, моніторинг температури, тиску та швидкості росту в режимі реального часу.
(3) Технологічні переваги
Високий коефіцієнт використання матеріалу: коефіцієнт перетворення сировини >70% (краще, ніж метод CVD).
Сумісність великих розмірів: досягнуто масового виробництва 6-дюймових дисплеїв, 8-дюймовий знаходиться на стадії розробки.
(4) Споживання енергії та вартість
Споживання енергії однією піччю становить 300~800 кВт·год, що становить 40%~60% собівартості виробництва SiC-підкладки.
Інвестиції в обладнання високі (1,5 млн 3 млн на одиницю), але вартість одиниці підкладки нижча, ніж при методі CVD.
Основні програми:
1. Силова електроніка: підкладка SiC MOSFET для інвертора електромобіля та фотоелектричного інвертора.
2. Радіочастотні пристрої: епітаксіальна підкладка GaN на SiC для базових станцій 5G (переважно 4H-SiC).
3. Прилади для екстремальних умов: датчики високої температури та високого тиску для аерокосмічного та ядерно-енергетичного обладнання.
Технічні параметри:
Специфікація | Деталі |
Розміри (Д × Ш × В) | 2500 × 2400 × 3456 мм або налаштувати |
Діаметр тигля | 900 мм |
Граничний вакуумний тиск | 6 × 10⁻⁴ Па (після 1,5 год вакууму) |
Коефіцієнт витоку | ≤5 Па/12 год (випікання) |
Діаметр вала обертання | 50 мм |
Швидкість обертання | 0,5–5 об/хв |
Спосіб нагрівання | Електричне нагрівання резистивним способом |
Максимальна температура печі | 2500°C |
Потужність опалення | 40 кВт × 2 × 20 кВт |
Вимірювання температури | Двоколірний інфрачервоний пірометр |
Діапазон температур | 900–3000°C |
Точність температури | ±1°C |
Діапазон тиску | 1–700 мбар |
Точність контролю тиску | 1–10 мбар: ±0,5% від повного діапазону; 10–100 мбар: ±0,5% від повного діапазону; 100–700 мбар: ±0,5% від повного діапазону |
Тип операції | Нижнє завантаження, ручні/автоматичні опції безпеки |
Додаткові функції | Подвійне вимірювання температури, кілька зон нагріву |
Послуги XKH:
Компанія XKH надає повний спектр послуг з виробництва печей SiC PVT, включаючи налаштування обладнання (розробка теплового поля, автоматичне керування), розробку процесу (контроль форми кристалів, оптимізація дефектів), технічне навчання (експлуатація та обслуговування) та післяпродажну підтримку (заміна графітових деталей, калібрування теплового поля), щоб допомогти клієнтам досягти високоякісного масового виробництва кристалів SiC. Ми також надаємо послуги з модернізації процесу для постійного підвищення виходу кристалів та ефективності їх вирощування, з типовим терміном виконання замовлення 3-6 місяців.
Детальна діаграма
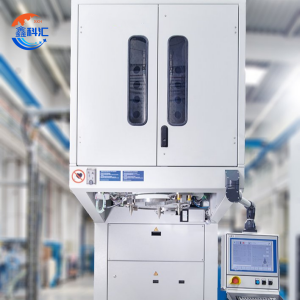
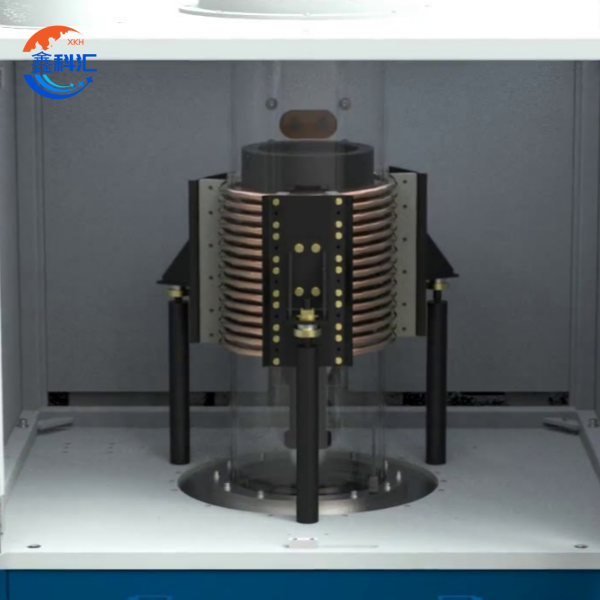
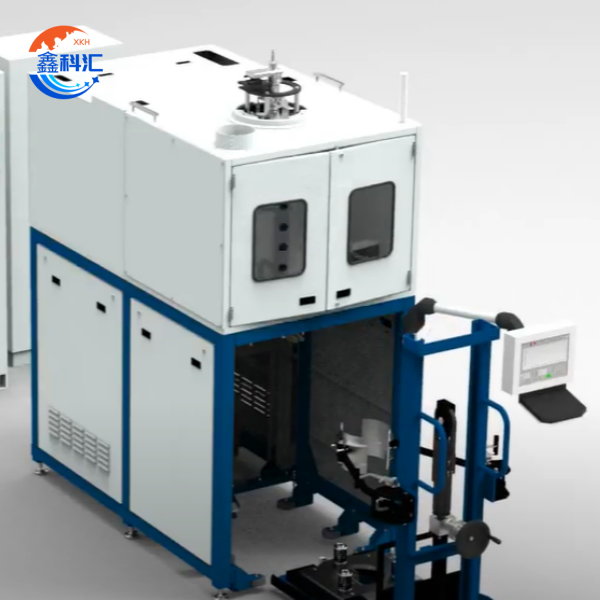