Технологія нарізання пластин, як критичний крок у процесі виробництва напівпровідників, безпосередньо пов'язана з продуктивністю, виходом та виробничими витратами чіпа.
#01 Передумови та значення нарізання вафель кубиками
1.1 Визначення нарізання вафель кубиками
Нарізка пластин (також відома як скрайбування) – це важливий етап у виробництві напівпровідників, спрямований на розділення оброблених пластин на кілька окремих кристалів. Ці кристали зазвичай містять повний спектр функціональних схем і є основними компонентами, які зрештою використовуються у виробництві електронних пристроїв. Оскільки конструкції мікросхем стають складнішими, а розміри продовжують зменшуватися, вимоги до точності та ефективності технології нарізки пластин стають дедалі суворішими.
На практиці для нарізання пластин зазвичай використовуються високоточні інструменти, такі як алмазні леза, щоб забезпечити цілісність та повну функціональність кожного штампа. Ключові кроки включають підготовку перед різанням, точний контроль під час процесу різання та перевірку якості після різання.
Перед різанням пластину необхідно позначити та розташувати, щоб забезпечити точні траєкторії різання. Під час різання такі параметри, як тиск інструменту та швидкість, необхідно суворо контролювати, щоб запобігти пошкодженню пластини. Після різання проводяться комплексні перевірки якості, щоб переконатися, що кожен чіп відповідає стандартам продуктивності.
Фундаментальні принципи технології нарізки пластин охоплюють не лише вибір ріжучого обладнання та встановлення параметрів процесу, але й вплив механічних властивостей та характеристик матеріалів на якість різання. Наприклад, кремнієві пластини з низьким коефіцієнтом діелектрика (low-k), через свої нижчі механічні властивості, дуже схильні до концентрації напружень під час різання, що призводить до таких пошкоджень, як відколи та розтріскування. Низька твердість та крихкість матеріалів з низьким коефіцієнтом диелектрика роблять їх більш схильними до структурних пошкоджень під дією механічних сил або термічних напружень, особливо під час різання. Контакт між інструментом та поверхнею пластини в поєднанні з високими температурами може ще більше посилити концентрацію напружень.
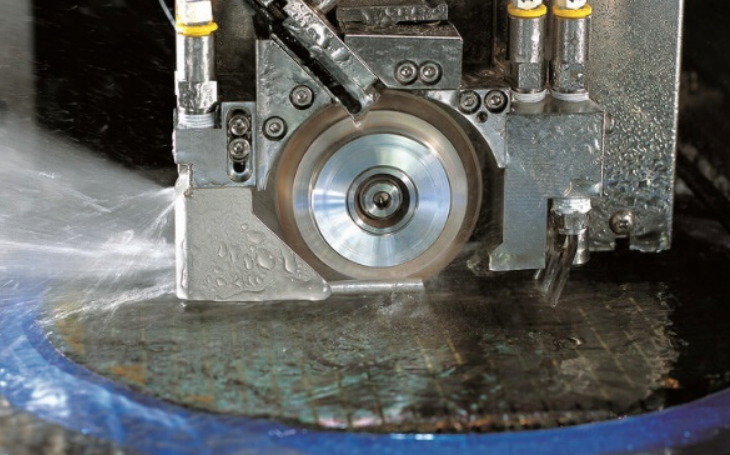
З розвитком матеріалознавства, технологія нарізки пластин вийшла за межі традиційних напівпровідників на основі кремнію та охопила нові матеріали, такі як нітрид галію (GaN). Ці нові матеріали, завдяки своїй твердості та структурним властивостям, створюють нові виклики для процесів нарізки, що вимагає подальшого вдосконалення ріжучих інструментів та методів.
Як критично важливий процес у напівпровідниковій промисловості, нарізка пластин продовжує оптимізуватися у відповідь на мінливі потреби та технологічний прогрес, закладаючи основу для майбутніх технологій мікроелектроніки та інтегральних схем.
Удосконалення технології нарізки пластин виходять за рамки розробки допоміжних матеріалів та інструментів. Вони також охоплюють оптимізацію процесів, підвищення продуктивності обладнання та точне керування параметрами нарізки. Ці досягнення спрямовані на забезпечення високої точності, ефективності та стабільності процесу нарізки пластин, задовольняючи потреби напівпровідникової промисловості в менших розмірах, вищій інтеграції та складніших структурах мікросхем.
зона покращення | Конкретні заходи | Ефекти |
Оптимізація процесів | - Покращення початкової підготовки, такої як точніше позиціонування пластини та планування шляху. | - Зменшення помилок різання та покращення стабільності. |
- Мінімізація помилок різання та підвищення стабільності. | - Впроваджуйте механізми моніторингу та зворотного зв'язку в режимі реального часу для регулювання тиску, швидкості та температури інструменту. | |
- Зниження рівня поломки пластини та покращення якості чіпа. | ||
Підвищення продуктивності обладнання | - Використовуйте високоточні механічні системи та передові технології автоматизованого керування. | - Підвищує точність різання та зменшує втрати матеріалу. |
- Впровадження технології лазерного різання, придатної для пластин з високотвердих матеріалів. | - Підвищити ефективність виробництва та зменшити кількість помилок, що виникають вручну. | |
- Підвищити автоматизацію обладнання для автоматичного моніторингу та налаштування. | ||
Точний контроль параметрів | - Точне налаштування параметрів, таких як глибина різання, швидкість, тип інструменту та методи охолодження. | - Забезпечити цілісність кристала та електричні характеристики. |
- Налаштування параметрів на основі матеріалу пластини, товщини та структури. | - Підвищення врожайності, зменшення відходів матеріалів та зниження виробничих витрат. | |
Стратегічне значення | - Постійно досліджувати нові технологічні шляхи, оптимізувати процеси та вдосконалювати можливості обладнання для задоволення потреб ринку. | - Покращення продуктивності та ефективності виробництва мікросхем, підтримка розробки нових матеріалів та передових конструкцій мікросхем. |
1.2 Важливість нарізання вафель кубиками
Нарізка пластин відіграє вирішальну роль у процесі виробництва напівпровідників, безпосередньо впливаючи на наступні кроки, а також на якість і продуктивність кінцевого продукту. Її важливість можна детально описати наступним чином:
По-перше, точність та послідовність нарізання є ключовими для забезпечення виходу та надійності чіпа. Під час виробництва пластини проходять кілька етапів обробки для формування численних складних схемних структур, які необхідно точно розділити на окремі чіпи (кристали). Якщо під час процесу нарізання є значні помилки в вирівнюванні або нарізанні, схеми можуть бути пошкоджені, що впливає на функціональність та надійність чіпа. Тому високоточна технологія нарізання не тільки забезпечує цілісність кожного чіпа, але й запобігає пошкодженню внутрішніх схем, покращуючи загальний коефіцієнт виходу.
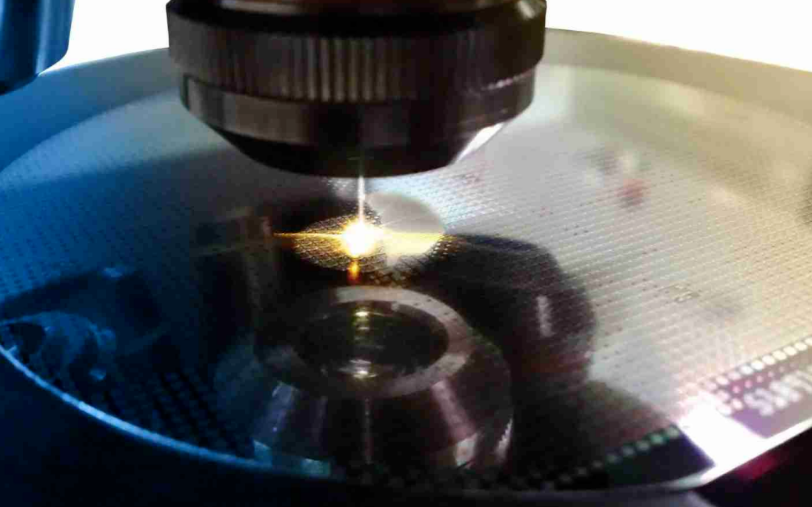
По-друге, нарізка пластин кубиками має значний вплив на ефективність виробництва та контроль витрат. Як вирішальний етап виробничого процесу, його ефективність безпосередньо впливає на перебіг наступних кроків. Оптимізуючи процес нарізки кубиками, підвищуючи рівень автоматизації та покращуючи швидкість різання, можна значно підвищити загальну ефективність виробництва.
З іншого боку, втрати матеріалу під час нарізання є критичним фактором в управлінні витратами. Використання передових технологій нарізання не тільки зменшує непотрібні втрати матеріалу під час процесу різання, але й збільшує коефіцієнт використання пластин, тим самим знижуючи виробничі витрати.
З розвитком напівпровідникових технологій діаметр пластин продовжує збільшуватися, а відповідно зростає і щільність схем, що ставить вищі вимоги до технології нарізки. Більші пластини вимагають точнішого контролю траєкторій різання, особливо в областях з високою щільністю схем, де навіть незначні відхилення можуть призвести до дефектів кількох мікросхем. Крім того, більші пластини передбачають більше ліній різання та складніші етапи процесу, що вимагає подальшого покращення точності, узгодженості та ефективності технологій нарізки для вирішення цих проблем.
1.3 Процес нарізання вафель кубиками
Процес нарізання вафель кубиками охоплює всі етапи, від підготовки до остаточної перевірки якості, причому кожен етап є критично важливим для забезпечення якості та експлуатаційних характеристик нарізаних чіпсів. Нижче наведено детальний опис кожного етапу.
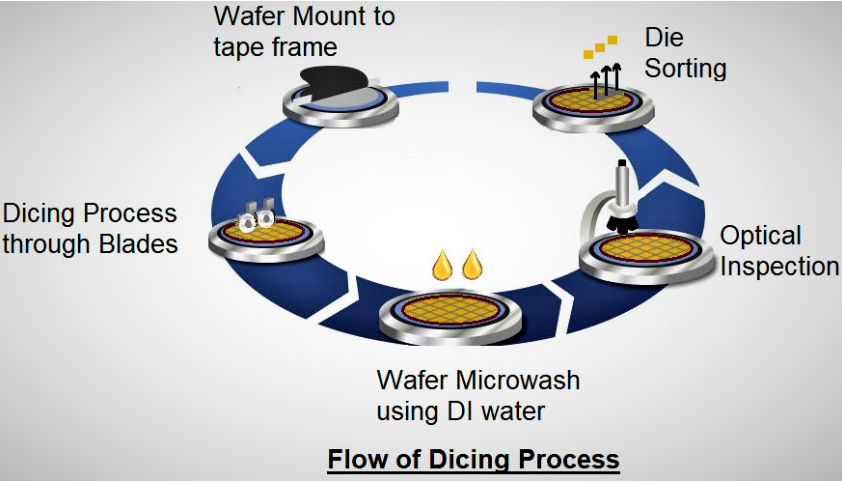
Фаза | Детальний опис |
Підготовча фаза | -Очищення пластинВикористовуйте високоочищену воду та спеціалізовані миючі засоби в поєднанні з ультразвуковим або механічним очищенням для видалення домішок, частинок та забруднень, забезпечуючи чисту поверхню. -Точне позиціонуванняВикористовуйте високоточне обладнання, щоб забезпечити точне розділення пластини вздовж розроблених траєкторій різання. -Фіксація пластинЗакріпіть пластину на стрічковій рамці, щоб забезпечити стабільність під час різання, запобігаючи пошкодженню від вібрації або руху. |
Фаза різання | -Нарізка кубиками лезомВикористовуйте високошвидкісні обертові леза з алмазним покриттям для фізичного різання, що підходять для кремнієвих матеріалів та є економічно ефективними. -Лазерне нарізання кубикамиВикористовуйте високоенергетичні лазерні промені для безконтактного різання, ідеально підходить для крихких або високотвердих матеріалів, таких як нітрид галію, забезпечуючи вищу точність та менші втрати матеріалу. -Нові технологіїВпровадження технологій лазерного та плазмового різання для подальшого підвищення ефективності та точності, одночасно мінімізуючи зони термічного впливу. |
Фаза очищення | - Використовуйте деіонізовану воду (DI воду) та спеціалізовані засоби для чищення в поєднанні з ультразвуковим або розпилювальним очищенням для видалення сміття та пилу, що утворюються під час різання, запобігаючи впливу залишків на подальші процеси або електричні характеристики стружки. - Високочиста деіонізована вода запобігає потраплянню нових забруднювачів, забезпечуючи чисте середовище для пластин. |
Фаза інспекції | -Оптичний оглядВикористовуйте оптичні системи виявлення в поєднанні з алгоритмами штучного інтелекту для швидкого виявлення дефектів, гарантуючи відсутність тріщин або сколів у нарізаній стружці, підвищуючи ефективність перевірки та зменшуючи кількість людських помилок. -Вимірювання розмірівПеревірте, чи відповідають розміри чіпа проектним вимогам. -Випробування електричних характеристикЗабезпечення відповідності електричних характеристик критично важливих мікросхем стандартам, що гарантує надійність у подальшому застосуванні. |
Фаза сортування | - Використовуйте роботизовані маніпулятори або вакуумні присоски для відділення кваліфікованих чіпів від стрічкової рами та автоматичного сортування їх залежно від продуктивності, забезпечуючи ефективність виробництва та гнучкість, а також підвищуючи точність. |
Процес різання пластин включає очищення, позиціонування, різання, очищення, перевірку та сортування пластин, причому кожен крок є критично важливим. Завдяки розвитку автоматизації, лазерного різання та технологій перевірки за допомогою штучного інтелекту, сучасні системи різання пластин можуть досягати вищої точності, швидкості та менших втрат матеріалу. У майбутньому нові технології різання, такі як лазерне та плазмове, поступово замінять традиційне різання лезами, щоб задовольнити потреби дедалі складніших конструкцій мікросхем, що ще більше стимулюватиме розвиток процесів виробництва напівпровідників.
Технологія різання пластин та її принципи
На зображенні показано три поширені технології різання пластин:Нарізка кубиками лезом,Лазерне нарізання кубиками, таПлазмове нарізання кубикамиНижче наведено детальний аналіз та додаткове пояснення цих трьох методів:
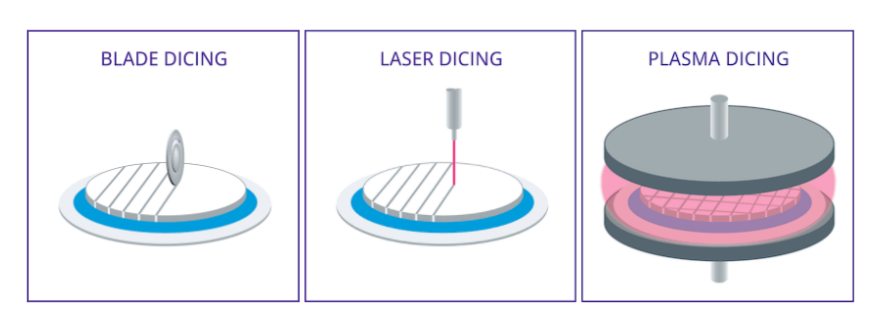
У виробництві напівпровідників різання пластин є вирішальним кроком, який вимагає вибору відповідного методу різання залежно від товщини пластини. Першим кроком є визначення товщини пластини. Якщо товщина пластини перевищує 100 мікрон, як метод різання можна обрати нарізання лезом. Якщо нарізання лезом не підходить, можна використовувати метод нарізання з розривом, який включає як техніку надрізного різання, так і техніку нарізання лезом.
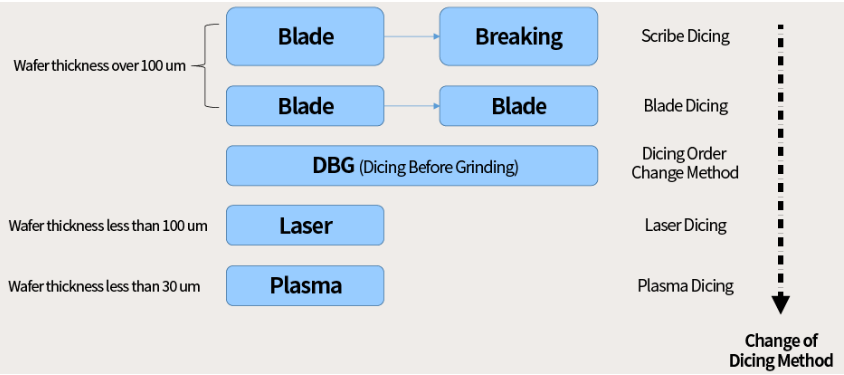
Коли товщина пластини становить від 30 до 100 мікрон, рекомендується метод DBG (Dice Before Grinding). У цьому випадку для досягнення найкращих результатів можна обрати надрізне різання, нарізання кубиками лезом або коригування послідовності різання за потреби.
Для надтонких пластин товщиною менше 30 мікрон лазерне різання стає кращим методом завдяки його здатності різати тонкі пластини точно, не завдаючи надмірних пошкоджень. Якщо лазерне різання не може задовольнити певні вимоги, як альтернативу можна використовувати плазмове різання. Ця блок-схема забезпечує чіткий шлях прийняття рішень, щоб забезпечити вибір найбільш підходящої технології різання пластин за різних умов товщини.
2.1 Технологія механічного різання
Технологія механічного різання є традиційним методом нарізання пластин кубиками. Основний принцип полягає у використанні високошвидкісного обертового алмазного шліфувального круга як ріжучого інструменту для нарізання пластини. Основне обладнання включає шпиндель з пневматичним підшипником, який приводить в рух алмазний шліфувальний круг з високою швидкістю для виконання точного різання або нарізання канавок вздовж заданої траєкторії різання. Ця технологія широко використовується в промисловості завдяки низькій вартості, високій ефективності та широкому застосуванню.
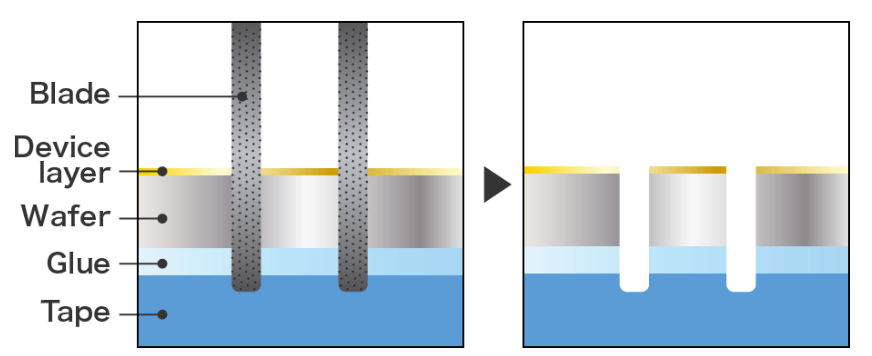
Переваги
Висока твердість та зносостійкість алмазних шліфувальних кругів дозволяють адаптувати технологію механічного різання до потреб різання різних матеріалів для пластин, як традиційних кремнієвих, так і новіших складних напівпровідників. Її експлуатація проста, з відносно низькими технічними вимогами, що ще більше сприяє її популярності в масовому виробництві. Крім того, порівняно з іншими методами різання, такими як лазерне різання, механічне різання має більш контрольовані витрати, що робить її придатною для потреб великосерійного виробництва.
Обмеження
Незважаючи на численні переваги, технологія механічного різання також має обмеження. По-перше, через фізичний контакт між інструментом та пластиною, точність різання відносно обмежена, що часто призводить до відхилень розмірів, які можуть вплинути на точність подальшого пакування та тестування мікросхем. По-друге, під час процесу механічного різання можуть легко виникнути такі дефекти, як відколи та тріщини, що не тільки впливає на коефіцієнт виходу, але й може негативно вплинути на надійність та термін служби мікросхем. Пошкодження, спричинені механічними напруженнями, особливо негативні для виробництва мікросхем високої щільності, особливо під час різання крихких матеріалів, де ці проблеми є більш вираженими.
Технологічні вдосконалення
Щоб подолати ці обмеження, дослідники постійно оптимізують процес механічного різання. Ключові вдосконалення включають удосконалення конструкції та вибору матеріалів шліфувальних кругів для підвищення точності та довговічності різання. Крім того, оптимізація структурної конструкції та систем керування різальним обладнанням ще більше покращила стабільність та автоматизацію процесу різання. Ці досягнення зменшують кількість помилок, спричинених людським впливом, та покращують стабільність різання. Впровадження передових технологій інспекції та контролю якості для моніторингу аномалій у режимі реального часу під час процесу різання також значно покращило надійність різання та вихід продукції.
Майбутній розвиток та нові технології
Хоча технологія механічного різання все ще займає значну позицію в різанні пластин, нові технології різання швидко розвиваються разом з розвитком напівпровідникових процесів. Наприклад, застосування технології термічного лазерного різання пропонує нові рішення для проблем точності та дефектів у механічному різанні. Цей безконтактний метод різання зменшує фізичне навантаження на пластину, значно знижуючи частоту відколів та розтріскування, особливо під час різання більш крихких матеріалів. У майбутньому інтеграція технології механічного різання з новими методами різання надасть виробництву напівпровідників більше можливостей та гнучкості, що ще більше підвищить ефективність виробництва та якість мікросхем.
На завершення, хоча технологія механічного різання має певні недоліки, постійні технологічні вдосконалення та її інтеграція з новими методами різання дозволяють їй і надалі відігравати важливу роль у виробництві напівпровідників та підтримувати свою конкурентоспроможність у майбутніх процесах.
2.2 Технологія лазерного різання
Технологія лазерного різання, як новий метод різання пластин, поступово отримала широку увагу в напівпровідниковій промисловості завдяки високій точності, відсутності механічних контактних пошкоджень та швидким можливостям різання. Ця технологія використовує високу щільність енергії та фокусуючу здатність лазерного променя для створення невеликої зони термічного впливу на поверхні матеріалу пластини. Коли лазерний промінь прикладається до пластини, утворене термічне напруження призводить до руйнування матеріалу в заданому місці, що забезпечує точне різання.
Переваги технології лазерного різання
• Висока точністьТочне позиціонування лазерного променя дозволяє досягати мікронної або навіть нанометрової точності різання, що відповідає вимогам сучасного високоточного виробництва інтегральних схем високої щільності.
• Без механічного контактуЛазерне різання дозволяє уникнути фізичного контакту з пластиною, запобігаючи поширеним проблемам механічного різання, таким як відколи та розтріскування, значно підвищуючи вихід продукції та надійність чіпів.
• Висока швидкість різанняВисока швидкість лазерного різання сприяє підвищенню ефективності виробництва, що робить його особливо придатним для масштабних, високошвидкісних виробничих сценаріїв.
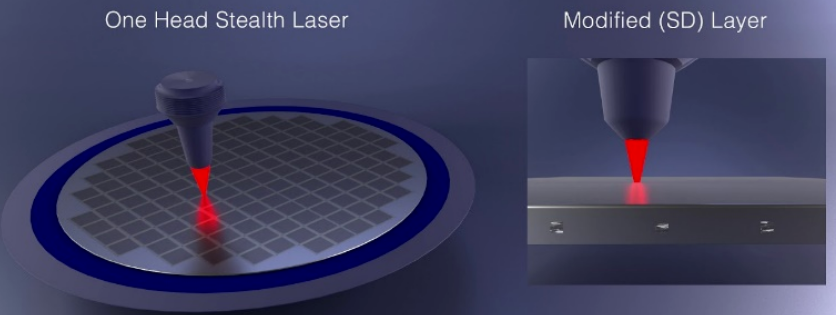
Виклики, з якими зіткнулися
• Висока вартість обладнанняПочаткові інвестиції в обладнання для лазерного різання є високими, що створює економічний тиск, особливо для малих та середніх виробничих підприємств.
• Комплексний контроль процесівЛазерне різання вимагає точного контролю кількох параметрів, включаючи щільність енергії, положення фокуса та швидкість різання, що робить процес складним.
• Проблеми зони впливу теплаХоча безконтактний характер лазерного різання зменшує механічні пошкодження, термічне напруження, спричинене зоною термічного впливу (ЗТВ), може негативно вплинути на властивості матеріалу пластини. Для мінімізації цього ефекту необхідна подальша оптимізація процесу.
Напрямки технологічного вдосконалення
Щоб вирішити ці проблеми, дослідники зосереджуються на зниженні вартості обладнання, підвищенні ефективності різання та оптимізації технологічного процесу.
• Ефективні лазери та оптичні системиРозробляючи ефективніші лазери та вдосконалені оптичні системи, можна знизити вартість обладнання, одночасно підвищуючи точність і швидкість різання.
• Оптимізація параметрів процесуПроводяться поглиблені дослідження взаємодії між лазерами та матеріалами пластин для вдосконалення процесів, що зменшують зону термічного впливу, тим самим покращуючи якість різання.
• Інтелектуальні системи керуванняРозробка інтелектуальних технологій керування спрямована на автоматизацію та оптимізацію процесу лазерного різання, покращення його стабільності та стабільності.
Технологія лазерного різання особливо ефективна для надтонких пластин та високоточних різань. Зі збільшенням розмірів пластин та підвищенням щільності схем, традиційні методи механічного різання намагаються задовольнити вимоги сучасного виробництва напівпровідників до високої точності та ефективності. Завдяки своїм унікальним перевагам, лазерне різання стає кращим рішенням у цих галузях.
Хоча технологія лазерного різання все ще стикається з такими проблемами, як висока вартість обладнання та складність процесу, її унікальні переваги у високій точності та безконтактному пошкодженні роблять її важливим напрямком розвитку у виробництві напівпровідників. Зі зростанням лазерних технологій та інтелектуальних систем керування очікується, що лазерне різання ще більше покращить ефективність та якість різання пластин, стимулюючи постійний розвиток напівпровідникової промисловості.
2.3 Технологія плазмового різання
Технологія плазмового різання, як новий метод нарізки пластин, привернула значну увагу в останні роки. Ця технологія використовує високоенергетичні плазмові промені для точного різання пластин, контролюючи енергію, швидкість та шлях різання плазмового променя, досягаючи оптимальних результатів різання.
Принцип роботи та переваги
Процес плазмового різання базується на високотемпературному, високоенергетичному плазмовому промені, що генерується обладнанням. Цей промінь може нагріти матеріал пластини до точки плавлення або випаровування за дуже короткий проміжок часу, що забезпечує швидке різання. Порівняно з традиційним механічним або лазерним різанням, плазмове різання відбувається швидше та створює меншу зону термічного впливу, що ефективно зменшує виникнення тріщин та пошкоджень під час різання.
У практичному застосуванні технологія плазмового різання особливо добре підходить для обробки пластин складної форми. Її високоенергетичний, регульований плазмовий промінь може легко різати пластини неправильної форми з високою точністю. Тому у виробництві мікроелектроніки, особливо у виробництві високоякісних мікросхем на замовлення та дрібносерійному виробництві, ця технологія має великі перспективи для широкого використання.
Проблеми та обмеження
Незважаючи на численні переваги технології плазмового різання, вона також стикається з деякими труднощами.
• Складний процесПроцес плазмового різання є складним і вимагає високоточного обладнання та досвідчених операторів для забезпеченняточність і стабільність різання.
• Контроль навколишнього середовища та безпекаВисокотемпературна та високоенергетична природа плазмового променя вимагає суворого контролю навколишнього середовища та заходів безпеки, що збільшує складність та вартість впровадження.
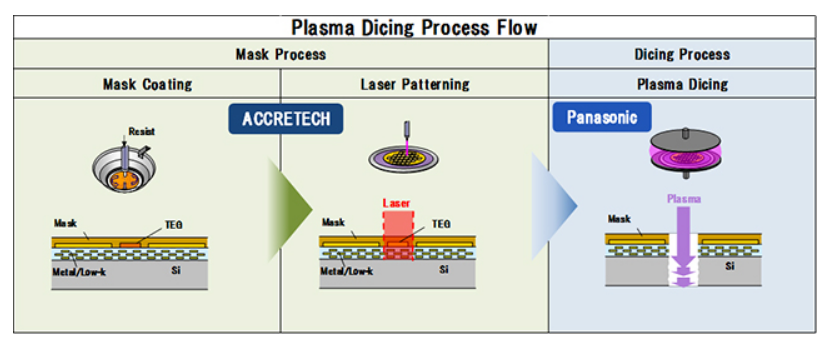
Напрямки майбутнього розвитку
Очікується, що з розвитком технологій проблеми, пов'язані з плазмовим різанням, будуть поступово подолані. Розробка більш розумного та стабільного різального обладнання дозволить зменшити залежність від ручного керування, тим самим підвищуючи ефективність виробництва. Водночас, оптимізація параметрів процесу та середовища різання допоможе знизити ризики для безпеки та експлуатаційні витрати.
У напівпровідниковій промисловості інновації в технології різання та нарізання пластин мають вирішальне значення для розвитку галузі. Технологія плазмового різання, завдяки високій точності, ефективності та здатності обробляти пластини складної форми, стала важливим новим гравцем у цій галузі. Хоча деякі проблеми залишаються, вони будуть поступово вирішуватися завдяки постійним технологічним інноваціям, що відкриває більше можливостей для виробництва напівпровідників.
Перспективи застосування технології плазмового різання величезні, і очікується, що в майбутньому вона відіграватиме дедалі важливішу роль у виробництві напівпровідників. Завдяки постійним технологічним інноваціям та оптимізації плазмове різання не лише вирішить існуючі проблеми, але й стане потужним рушієм зростання напівпровідникової промисловості.
2.4 Якість різання та фактори впливу
Якість різання пластин має вирішальне значення для подальшого пакування мікросхем, тестування, а також загальної продуктивності та надійності кінцевого продукту. До поширених проблем, що виникають під час різання, належать тріщини, відколи та відхилення від різання. На ці проблеми впливає кілька факторів, що діють разом.
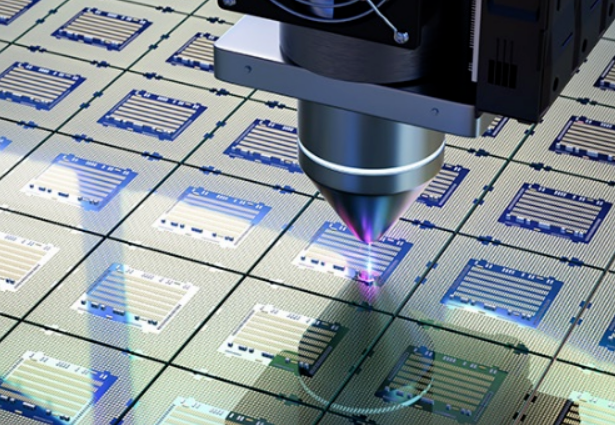
Категорія | Зміст | Вплив |
Параметри процесу | Швидкість різання, швидкість подачі та глибина різання безпосередньо впливають на стабільність і точність процесу різання. Неправильне налаштування може призвести до концентрації напружень і надмірного утворення зони термічного впливу, що спричиняє тріщини та відколи. Відповідне налаштування параметрів залежно від матеріалу пластини, товщини та вимог до різання є ключем до досягнення бажаних результатів різання. | Правильні параметри процесу забезпечують точне різання та зменшують ризик виникнення дефектів, таких як тріщини та відколи. |
Фактори обладнання та матеріалів | -Якість лезаМатеріал, твердість та зносостійкість леза впливають на плавність процесу різання та площинність поверхні різу. Леза низької якості збільшують тертя та термічне напруження, що може призвести до тріщин або сколів. Вибір правильного матеріалу леза має вирішальне значення. -Продуктивність охолоджувальної рідиниОхолоджувальні рідини допомагають знизити температуру різання, мінімізувати тертя та видаляти сміття. Неефективна охолоджувальна рідина може призвести до високих температур та накопичення сміття, що впливає на якість та ефективність різання. Вибір ефективних та екологічно чистих охолоджувальних рідин є життєво важливим. | Якість леза впливає на точність і плавність різу. Неефективна охолоджувальна рідина може призвести до низької якості різу та ефективності, що підкреслює необхідність оптимального використання охолоджувальної рідини. |
Контроль процесів та перевірка якості | -Контроль процесівМоніторинг та налаштування ключових параметрів різання в режимі реального часу для забезпечення стабільності та послідовності процесу різання. -Перевірка якостіПеревірка зовнішнього вигляду після різання, вимірювання розмірів та випробування електричних характеристик допомагають швидко виявляти та усувати проблеми з якістю, покращуючи точність та стабільність різання. | Належний контроль процесу та перевірка якості допомагають забезпечити стабільні, високоякісні результати різання та раннє виявлення потенційних проблем. |

Покращення якості різання
Покращення якості різання вимагає комплексного підходу, який враховує параметри процесу, вибір обладнання та матеріалів, контроль процесу та перевірку. Завдяки постійному вдосконаленню технологій різання та оптимізації методів процесу можна ще більше підвищити точність і стабільність різання пластин, забезпечуючи надійнішу технічну підтримку для виробництва напівпровідників.
#03 Обробка та тестування після різання
3.1 Очищення та сушіння
Етапи очищення та сушіння після різання пластини є критично важливими для забезпечення якості чіпа та безперебійного перебігу наступних процесів. На цьому етапі важливо ретельно видалити кремнієві залишки, залишки охолоджувальної рідини та інші забруднення, що утворюються під час різання. Так само важливо переконатися, що чіпи не пошкоджені під час процесу очищення, а після сушіння переконатися, що на поверхні чіпа не залишилося вологи, щоб запобігти таким проблемам, як корозія або електростатичний розряд.
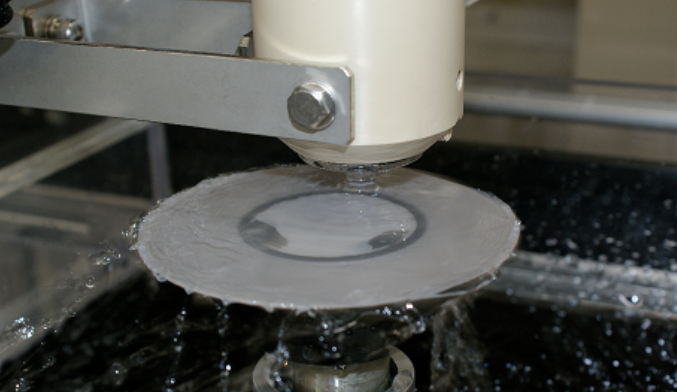
Обробка після різання: процес очищення та сушіння
Крок процесу | Зміст | Вплив |
Процес очищення | -МетодВикористовуйте спеціальні засоби для чищення та чисту воду в поєднанні з ультразвуковими або механічними методами чищення. | Забезпечує ретельне видалення забруднень та запобігає пошкодженню стружки під час очищення. |
-Вибір засобу для чищенняВибирайте на основі матеріалу пластини та типу забруднення, щоб забезпечити ефективне очищення без пошкодження чіпа. | Правильний вибір засобу є ключем до ефективного очищення та захисту від стружки. | |
-Контроль параметрівСуворо контролюйте температуру, час та концентрацію миючого розчину, щоб запобігти проблемам із якістю, спричиненим неправильним очищенням. | Контроль допомагає уникнути пошкодження пластини або забруднення, забезпечуючи стабільну якість. | |
Процес сушіння | -Традиційні методиПриродне сушіння повітрям та сушіння гарячим повітрям, які мають низьку ефективність і можуть призвести до накопичення статичної електрики. | Може призвести до уповільнення часу висихання та потенційних проблем зі статичною електрикою. |
-Сучасні технологіїВикористовуйте передові технології, такі як вакуумне сушіння та інфрачервоне сушіння, щоб забезпечити швидке висихання стружки та уникнути шкідливого впливу. | Швидший та ефективніший процес сушіння, що зменшує ризик статичного розряду або проблем, пов'язаних з вологою. | |
Вибір та обслуговування обладнання | -Вибір обладнанняВисокопродуктивні машини для очищення та сушіння підвищують ефективність обробки та точно контролюють потенційні проблеми під час обробки. | Високоякісні машини забезпечують кращу обробку та зменшують ймовірність помилок під час очищення та сушіння. |
-Технічне обслуговування обладнанняРегулярний огляд та технічне обслуговування обладнання забезпечують його оптимальний робочий стан, гарантуючи якість стружки. | Правильне технічне обслуговування запобігає поломкам обладнання, забезпечуючи надійну та високоякісну обробку. |
Очищення та сушіння після різання
Етапи очищення та сушіння після різання пластини – це складні та делікатні процеси, які вимагають ретельного врахування багатьох факторів для забезпечення кінцевого результату обробки. Використовуючи наукові методи та суворі процедури, можна гарантувати, що кожен чіп потрапляє на наступні етапи упаковки та тестування в оптимальному стані.
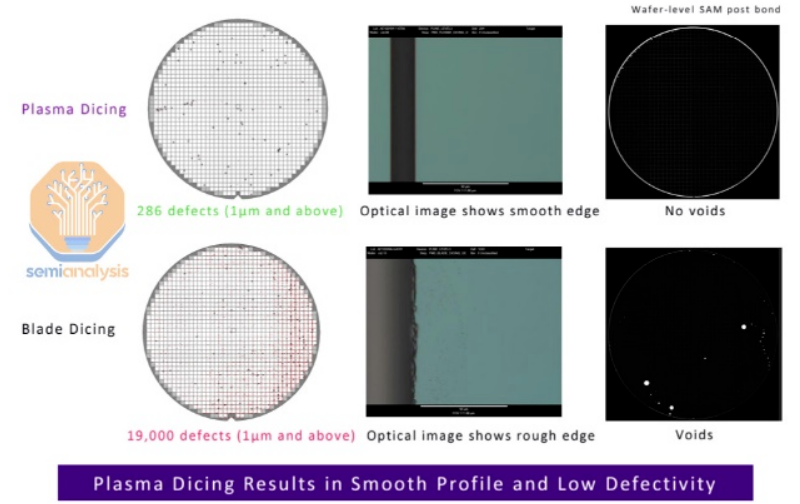
Інспекція та випробування після різання
Крок | Зміст | Вплив |
Крок перевірки | 1.Візуальний оглядВикористовуйте візуальне або автоматизоване обладнання для перевірки на наявність видимих дефектів, таких як тріщини, відколи або забруднення на поверхні стружки. Швидко виявляйте фізично пошкоджену стружку, щоб уникнути відходів. | Допомагає виявляти та усувати дефектну стружку на ранніх етапах процесу, зменшуючи втрати матеріалу. |
2.Вимірювання розміруВикористовуйте прецизійні вимірювальні прилади для точного вимірювання розмірів чіпа, забезпечуючи відповідність розміру різу проектним вимогам та запобігаючи проблемам з продуктивністю або труднощам з упаковкою. | Забезпечує відповідність розмірів мікросхем необхідним нормам, запобігаючи зниженню продуктивності або проблемам зі складанням. | |
3.Випробування електричних характеристикОцінити ключові електричні параметри, такі як опір, ємність та індуктивність, щоб виявити невідповідні мікросхеми та забезпечити, щоб до наступного етапу переходили лише ті, що відповідають вимогам щодо продуктивності. | Забезпечує використання лише функціональних та перевірених на працездатність мікросхем у процесі, зменшуючи ризик збоїв на пізніших етапах. | |
Крок тестування | 1.Функціональне тестуванняПеревірка належного функціонування основної функціональності чіпа, виявлення та усунення чіпів з функціональними порушеннями. | Забезпечує відповідність чіпів основним експлуатаційним вимогам перед переходом до наступних етапів. |
2.Тестування надійностіОцінка стабільності продуктивності мікросхеми за тривалого використання або в суворих умовах, зазвичай включаючи старіння при високих температурах, випробування за низьких температур та випробування на вологість для імітації реальних екстремальних умов. | Забезпечує надійну роботу мікросхем за різних умов навколишнього середовища, підвищуючи довговічність та стабільність продукту. | |
3.Тестування сумісностіПеревірте, чи чіп належним чином працює з іншими компонентами або системами, гарантуючи відсутність несправностей або погіршення продуктивності через несумісність. | Забезпечує безперебійну роботу в реальних програмах, запобігаючи проблемам сумісності. |
3.3 Упаковка та зберігання
Після нарізання пластин, мікросхеми є важливим продуктом виробництва напівпровідників, і етапи їх пакування та зберігання не менш важливі. Належні заходи пакування та зберігання є важливими не лише для забезпечення безпеки та стабільності мікросхем під час транспортування та зберігання, але й для забезпечення надійної підтримки на наступних етапах виробництва, тестування та пакування.
Короткий опис етапів перевірки та випробування:
Етапи перевірки та тестування мікросхем після різання пластин охоплюють низку аспектів, включаючи візуальний огляд, вимірювання розмірів, тестування електричних характеристик, функціональне тестування, тестування надійності та тестування сумісності. Ці кроки взаємопов'язані та доповнюють один одного, утворюючи надійний бар'єр для забезпечення якості та надійності продукції. Завдяки суворим процедурам перевірки та тестування потенційні проблеми можна виявити та швидко вирішити, гарантуючи, що кінцевий продукт відповідає вимогам та очікуванням замовника.
Аспект | Зміст |
Заходи з упаковки | 1.АнтистатичнийПакувальні матеріали повинні мати відмінні антистатичні властивості, щоб запобігти пошкодженню пристроїв або впливу на їхню роботу статичною електрикою. |
2.ВологостійкийПакувальні матеріали повинні мати добру вологостійкість, щоб запобігти корозії та погіршенню електричних характеристик, спричиненим вологістю. | |
3.УдаростійкийПакувальні матеріали повинні забезпечувати ефективну амортизацію для захисту чіпсів від вібрації та ударів під час транспортування. | |
Середовище зберігання | 1.Контроль вологостіСуворо контролюйте вологість у відповідному діапазоні, щоб запобігти поглинанню вологи та корозії, спричиненій надмірною вологістю, або статичним проблемам, спричиненим низькою вологістю. |
2.ЧистотаПідтримуйте чисте середовище для зберігання, щоб уникнути забруднення стружки пилом та сторонніми сторонніми сторонами. | |
3.Контроль температуриВстановіть розумний діапазон температур і підтримуйте стабільність температури, щоб запобігти прискореному старінню через надмірне нагрівання або проблеми з конденсацією, спричинені низькими температурами. | |
Регулярна перевірка | Регулярно перевіряйте та оцінюйте чіпи, що зберігаються, використовуючи візуальний огляд, вимірювання розмірів та випробування електричних характеристик, щоб своєчасно виявляти та усувати потенційні проблеми. Виходячи з часу та умов зберігання, плануйте використання чіпів, щоб забезпечити їх використання в оптимальному стані. |
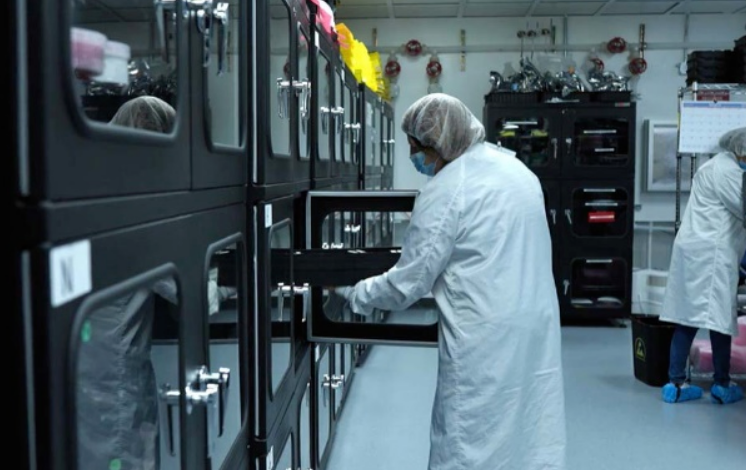
Проблема мікротріщин та пошкоджень під час процесу нарізки пластин є значною проблемою у виробництві напівпровідників. Різальна напруга є основною причиною цього явища, оскільки вона створює крихітні тріщини та пошкодження на поверхні пластини, що призводить до збільшення виробничих витрат та зниження якості продукції.
Для вирішення цієї проблеми вкрай важливо мінімізувати напругу різання та впроваджувати оптимізовані методи різання, інструменти та умови. Пильна увага до таких факторів, як матеріал леза, швидкість різання, тиск і методи охолодження, може допомогти зменшити утворення мікротріщин і підвищити загальний вихід процесу. Крім того, постійні дослідження більш просунутих технологій різання, таких як лазерне нарізання кубиками, вивчають шляхи подальшого пом'якшення цих проблем.
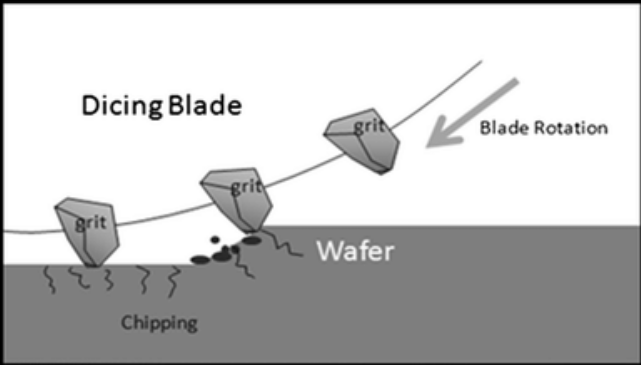
Як крихкий матеріал, пластини схильні до внутрішніх структурних змін під впливом механічних, термічних або хімічних навантажень, що призводить до утворення мікротріщин. Хоча ці тріщини можуть бути не помітні одразу, вони можуть розширюватися та завдавати серйозніших пошкоджень у міру розвитку виробничого процесу. Ця проблема стає особливо проблематичною на наступних етапах пакування та тестування, де коливання температури та додаткові механічні навантаження можуть призвести до перетворення цих мікротріщин на видимі розломи, що потенційно може призвести до руйнування чіпа.
Щоб зменшити цей ризик, важливо ретельно контролювати процес різання, оптимізуючи такі параметри, як швидкість різання, тиск і температура. Використання менш агресивних методів різання, таких як лазерне нарізання, може зменшити механічне навантаження на пластину та мінімізувати утворення мікротріщин. Крім того, впровадження передових методів контролю, таких як інфрачервоне сканування або рентгенівське зображення, під час процесу нарізання пластини може допомогти виявити ці тріщини на ранній стадії, перш ніж вони спричинять подальші пошкодження.
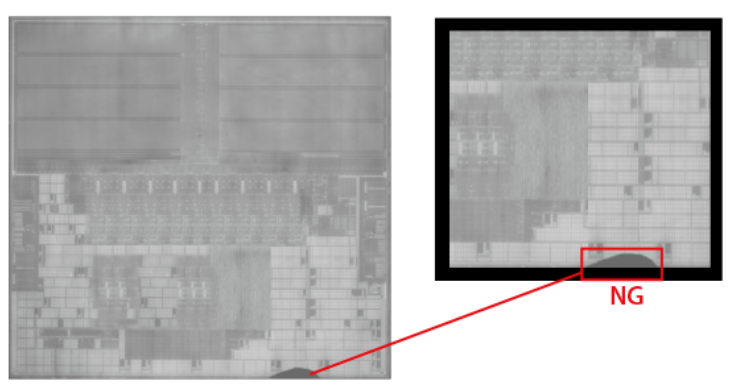
Пошкодження поверхні пластини є суттєвою проблемою в процесі нарізки, оскільки це може безпосередньо впливати на продуктивність та надійність чіпа. Такі пошкодження можуть бути спричинені неправильним використанням ріжучих інструментів, неправильними параметрами різання або дефектами матеріалу, властивими самій пластині. Незалежно від причини, ці пошкодження можуть призвести до змін електричного опору або ємності схеми, що впливає на загальну продуктивність.
Для вирішення цих проблем досліджуються дві ключові стратегії:
1. Оптимізація ріжучих інструментів та параметрівВикористовуючи гостріші леза, регулюючи швидкість різання та змінюючи глибину різання, можна мінімізувати концентрацію напружень під час процесу різання, тим самим зменшуючи потенційну можливість пошкодження.
2. Вивчення нових технологій різанняПередові методи, такі як лазерне та плазмове різання, забезпечують підвищену точність, потенційно зменшуючи рівень пошкодження пластини. Ці технології вивчаються з метою пошуку способів досягнення високої точності різання, мінімізуючи при цьому термічні та механічні навантаження на пластину.
Площа теплового впливу та її вплив на продуктивність
У процесах термічного різання, таких як лазерне та плазмове різання, високі температури неминуче створюють зону термічного впливу на поверхні пластини. Ця область, де градієнт температури є значним, може змінити властивості матеріалу, впливаючи на кінцеву продуктивність чіпа.
Вплив зони термічного впливу (ЗТВ):
Зміни кристалічної структуриПід впливом високих температур атоми в матеріалі пластини можуть перебудовуватися, що призводить до спотворень кристалічної структури. Це спотворення послаблює матеріал, зменшуючи його механічну міцність і стабільність, що збільшує ризик виходу з ладу чіпа під час використання.
Зміни електричних властивостейВисокі температури можуть змінювати концентрацію та рухливість носіїв заряду в напівпровідникових матеріалах, впливаючи на електропровідність мікросхеми та ефективність передачі струму. Ці зміни можуть призвести до зниження продуктивності мікросхеми, що потенційно може зробити її непридатною для використання за призначенням.
Щоб пом'якшити ці наслідки, контроль температури під час різання, оптимізація параметрів різання та дослідження таких методів, як охолоджувальні струмені або подальша обробка, є важливими стратегіями для зменшення ступеня термічного впливу та збереження цілісності матеріалу.
Загалом, як мікротріщини, так і зони термічного удару є вирішальними проблемами в технології нарізки пластин. Для покращення якості напівпровідникової продукції та підвищення її конкурентоспроможності на ринку необхідні подальші дослідження, поряд з технологічним прогресом та заходами контролю якості.
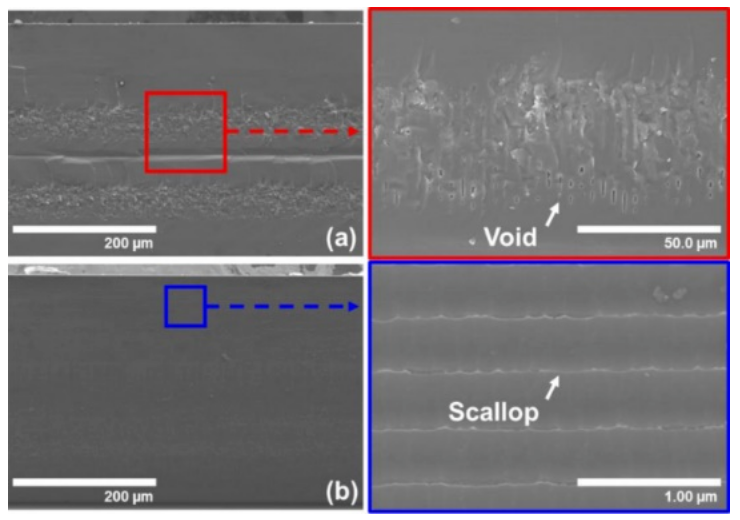
Заходи щодо контролю зони термічного впливу:
Оптимізація параметрів процесу різанняЗменшення швидкості та потужності різання може ефективно мінімізувати розмір зони термічного удару (TAZ). Це допомагає контролювати кількість тепла, що утворюється під час процесу різання, що безпосередньо впливає на властивості матеріалу пластини.
Передові технології охолодженняЗастосування таких технологій, як охолодження рідким азотом та мікрофлюїдне охолодження, може значно обмежити діапазон зони термічного впливу. Ці методи охолодження допомагають ефективніше розсіювати тепло, тим самим зберігаючи властивості матеріалу пластини та мінімізуючи термічні пошкодження.
Вибір матеріалуДослідники досліджують нові матеріали, такі як вуглецеві нанотрубки та графен, які мають чудову теплопровідність та механічну міцність. Ці матеріали можуть зменшити зону теплового удару, одночасно покращуючи загальну продуктивність чіпів.
Підсумовуючи, хоча зона термічного впливу є неминучим наслідком технологій термічного різання, її можна ефективно контролювати за допомогою оптимізованих методів обробки та вибору матеріалів. Майбутні дослідження, ймовірно, будуть зосереджені на точному налаштуванні та автоматизації процесів термічного різання для досягнення більш ефективного та точного нарізання пластин.

Стратегія балансу:
Досягнення оптимального балансу між виходом пластин та ефективністю виробництва є постійним викликом у технології нарізки пластин. Виробникам необхідно враховувати численні фактори, такі як ринковий попит, виробничі витрати та якість продукції, щоб розробити раціональну виробничу стратегію та параметри процесу. Водночас, впровадження передового різального обладнання, підвищення кваліфікації операторів та покращення контролю якості сировини є важливими для підтримки або навіть підвищення виходу, одночасно підвищуючи ефективність виробництва.
Майбутні виклики та можливості:
З розвитком напівпровідникових технологій різання пластин стикається з новими викликами та можливостями. Зі зменшенням розмірів мікросхем та збільшенням інтеграції вимоги до точності та якості різання значно зростають. Одночасно нові технології пропонують нові ідеї для розробки методів різання пластин. Виробники повинні бути в курсі динаміки ринку та технологічних тенденцій, постійно коригуючи та оптимізуючи виробничі стратегії та параметри процесу, щоб відповідати змінам ринку та технологічним вимогам.
На завершення, враховуючи ринковий попит, виробничі витрати та якість продукції, а також впроваджуючи передове обладнання та технології, підвищуючи кваліфікацію операторів та посилюючи контроль сировини, виробники можуть досягти найкращого балансу між виходом пластин та ефективністю виробництва під час нарізки пластин, що призводить до ефективного та високоякісного виробництва напівпровідникової продукції.
Перспективи на майбутнє:
Зі швидким технологічним прогресом, напівпровідникові технології розвиваються безпрецедентними темпами. Як критичний крок у виробництві напівпровідників, технологія різання пластин готова до захопливих нових розробок. Заглядаючи в майбутнє, очікується, що технологія різання пластин досягне значних покращень у точності, ефективності та вартості, надаючи нового імпульсу подальшому зростанню напівпровідникової промисловості.
Підвищення точності:
У прагненні до вищої точності, технологія різання пластин постійно розширюватиме межі існуючих процесів. Завдяки глибокому вивченню фізичних та хімічних механізмів процесу різання та точному контролю параметрів різання, будуть досягнуті точніші результати різання, що відповідають дедалі складнішим вимогам до проектування схем. Крім того, дослідження нових матеріалів та методів різання значно покращить вихід продукції та якість.
Підвищення ефективності:
Нове обладнання для різання пластин буде зосереджено на інтелектуальному та автоматизованому проектуванні. Впровадження передових систем керування та алгоритмів дозволить обладнанню автоматично регулювати параметри різання відповідно до різних матеріалів та вимог до дизайну, тим самим значно підвищуючи ефективність виробництва. Такі інновації, як технологія різання кількох пластин та системи швидкої заміни лез, відіграватимуть вирішальну роль у підвищенні ефективності.
Зменшення витрат:
Зниження витрат є ключовим напрямком розвитку технології різання пластин. З розробкою нових матеріалів та методів різання очікується ефективний контроль витрат на обладнання та витрати на обслуговування. Крім того, оптимізація виробничих процесів та зниження рівня браку ще більше зменшать відходи під час виробництва, що призведе до зниження загальних виробничих витрат.
Розумне виробництво та Інтернет речей:
Інтеграція технологій розумного виробництва та Інтернету речей (IoT) принесе трансформаційні зміни в технологію різання пластин. Завдяки взаємозв'язку та обміну даними між пристроями, кожен етап виробничого процесу можна контролювати та оптимізувати в режимі реального часу. Це не тільки підвищує ефективність виробництва та якість продукції, але й забезпечує компаніям точніше прогнозування ринку та підтримку прийняття рішень.
У майбутньому технологія різання пластин досягне значного прогресу в точності, ефективності та вартості. Ці досягнення сприятимуть подальшому розвитку напівпровідникової промисловості та принесуть більше технологічних інновацій та зручностей людському суспільству.
Час публікації: 19 листопада 2024 р.