Вступ до карбіду кремнію
Карбід кремнію (SiC) – це напівпровідниковий матеріал, що складається з вуглецю та кремнію, який є одним із ідеальних матеріалів для виготовлення високотемпературних, високочастотних, потужних та високовольтних пристроїв. Порівняно з традиційним кремнієвим матеріалом (Si), ширина забороненої зони карбіду кремнію в 3 рази більша, ніж у кремнію. Теплопровідність у 4-5 разів більша, ніж у кремнію; напруга пробою у 8-10 разів більша, ніж у кремнію; швидкість електронного дрейфу насичення в 2-3 рази більша, ніж у кремнію, що відповідає потребам сучасної промисловості у високій потужності, високій напрузі та високій частоті. Він в основному використовується для виробництва високошвидкісних, високочастотних, потужних та світловипромінюючих електронних компонентів. Галузі застосування включають інтелектуальні мережі, транспортні засоби нової енергії, фотоелектричну вітроенергетику, зв'язок 5G тощо. Карбідкремнієві діоди та MOSFET знайшли комерційне застосування.
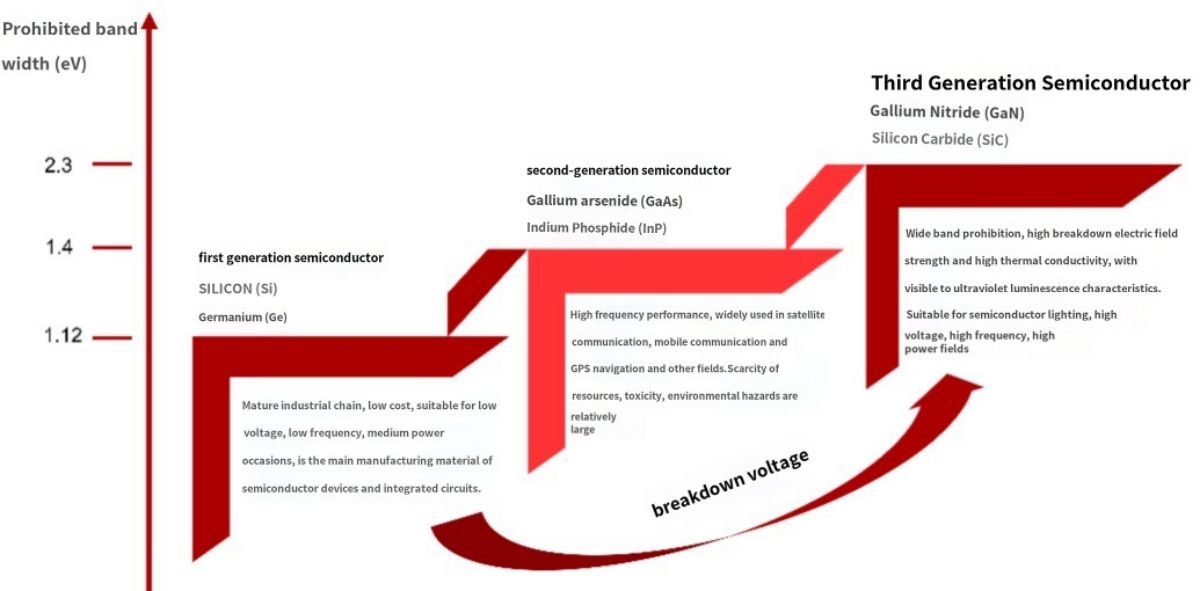
Стійкість до високих температур. Ширина забороненої зони карбіду кремнію в 2-3 рази більша, ніж у кремнію, електрони нелегко переходять за високих температур і можуть витримувати вищі робочі температури, а теплопровідність карбіду кремнію в 4-5 разів більша, ніж у кремнію, що полегшує розсіювання тепла пристроєм і підвищує граничну робочу температуру. Стійкість до високих температур може значно збільшити щільність потужності, одночасно знижуючи вимоги до системи охолодження, роблячи термінал легшим і меншим.
Витримують високий тиск. Напруженість пробивного електричного поля карбіду кремнію в 10 разів вища, ніж у кремнію, який може витримувати вищі напруги та більше підходить для високовольтних пристроїв.
Високочастотний опір. Карбід кремнію має швидкість дрейфу електронів насичення вдвічі більшу, ніж кремній, що призводить до відсутності хвостів струму під час процесу вимкнення, що може ефективно покращити частоту перемикання пристрою та реалізувати його мініатюризацію.
Низькі втрати енергії. Порівняно з кремнієвим матеріалом, карбід кремнію має дуже низький опір увімкнення та низькі втрати увімкнення. Водночас, велика ширина забороненої зони карбіду кремнію значно зменшує струм витоку та втрати потужності. Крім того, у карбід-кремнієвому пристрої немає явища затримки струму під час процесу вимкнення, а втрати на перемикання низькі.
Ланцюг промисловості карбіду кремнію
Це в основному включає підкладку, епітаксію, проектування пристрою, виробництво, герметизацію тощо. Карбід кремнію від матеріалу до напівпровідникового силового пристрою проходить через вирощування монокристалів, нарізання злитків, епітаксіальне вирощування, проектування пластини, виробництво, упаковку та інші процеси. Після синтезу порошку карбіду кремнію спочатку виготовляють злиток карбіду кремнію, потім підкладку з карбіду кремнію отримують шляхом нарізання, шліфування та полірування, а епітаксіальний лист отримують шляхом епітаксіального вирощування. Епітаксіальна пластина виготовляється з карбіду кремнію за допомогою літографії, травлення, іонної імплантації, пасивації металу та інших процесів, пластина розрізається на кристалл, пристрій упаковується, а потім пристрій об'єднується в спеціальну оболонку та збирається в модуль.
Вгору по ланцюжку промисловості 1: субстрат - ріст кристалів є основною ланкою процесу
Підкладка з карбіду кремнію становить близько 47% вартості пристроїв з карбіду кремнію, що має найвищі технічні бар'єри у виробництві та найбільшу вартість, і є основою майбутньої великомасштабної індустріалізації SiC.
З точки зору відмінностей в електрохімічних властивостях, матеріали для підкладок з карбіду кремнію можна розділити на провідні підкладки (область питомого опору 15~30 мОм·см) та напівізольовані підкладки (питомий опір вище 105 Ом·см). Ці два типи підкладок використовуються для виготовлення дискретних пристроїв, таких як силові пристрої та радіочастотні пристрої відповідно, після епітаксіального вирощування. Серед них напівізольована підкладка з карбіду кремнію в основному використовується у виробництві радіочастотних пристроїв з нітриду галію, фотоелектричних пристроїв тощо. Шляхом вирощування епітаксіального шару gan на напівізольованій підкладці SIC готується епітаксіальна пластина sic, яку можна додатково переробити в радіочастотні пристрої з ізонітриду gan HEMT. Провідна підкладка з карбіду кремнію в основному використовується у виробництві силових пристроїв. На відміну від традиційного процесу виробництва кремнієвих силових пристроїв, силові пристрої з карбіду кремнію не можуть бути виготовлені безпосередньо на підкладці з карбіду кремнію, епітаксіальний шар карбіду кремнію необхідно вирощувати на провідній підкладці для отримання епітаксіального листа карбіду кремнію, а епітаксіальний шар виготовляється на діодах Шотткі, MOSFET, IGBT та інших силових пристроях.
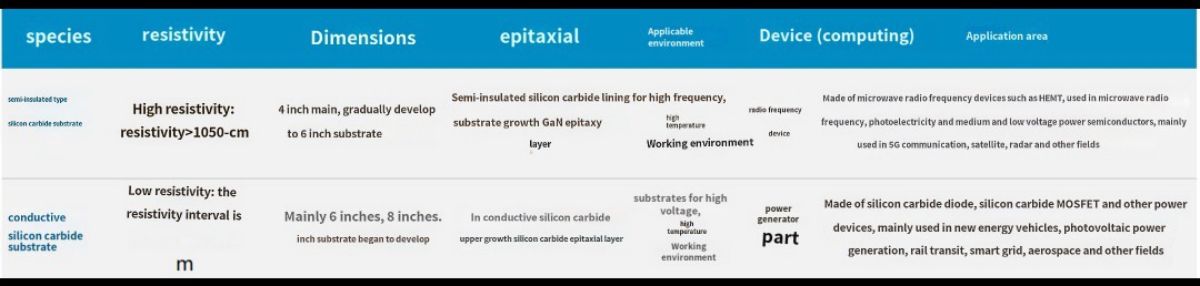
Порошок карбіду кремнію був синтезований з порошку високочистого вуглецю та порошку високочистого кремнію, а злитки карбіду кремнію різних розмірів були вирощені в спеціальному температурному полі, а потім підкладка з карбіду кремнію була отримана за допомогою кількох процесів обробки. Основний процес включає:
Синтез сировини: Високочистий кремнієвий порошок + тонер змішуються згідно з формулою, і реакція проводиться в реакційній камері за високої температури понад 2000°C для синтезу частинок карбіду кремнію з певним типом кристалів та розміром частинок. Потім за допомогою дроблення, просіювання, очищення та інших процесів, що відповідає вимогам до високочистої сировини - порошку карбіду кремнію.
Вирощування кристалів є основним процесом виробництва підкладки з карбіду кремнію, який визначає електричні властивості підкладки з карбіду кремнію. Наразі основними методами вирощування кристалів є фізичний перенос парової фази (PVT), високотемпературне хімічне осадження з парової фази (HT-CVD) та рідкофазна епітаксія (LPE). Серед них метод PVT є основним методом комерційного вирощування підкладки SiC наразі, має найвищу технічну зрілість та найбільш широко використовується в техніці.
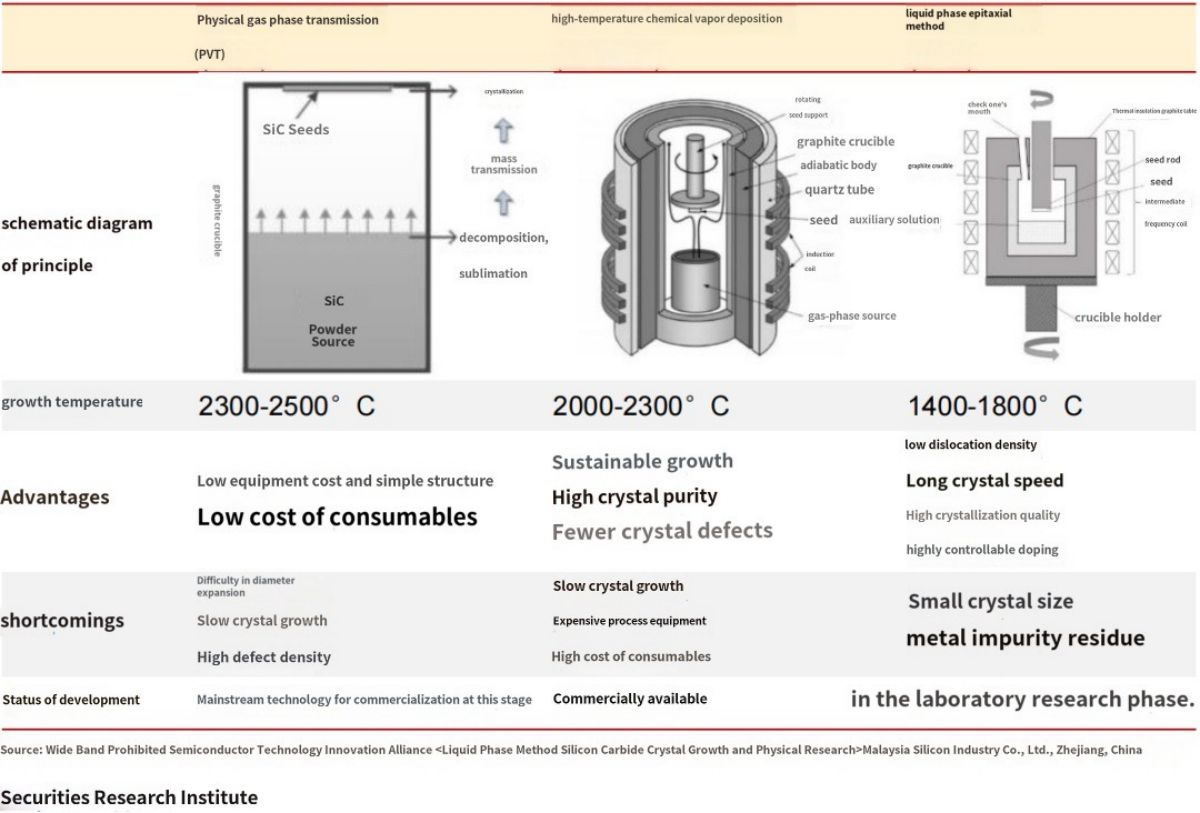
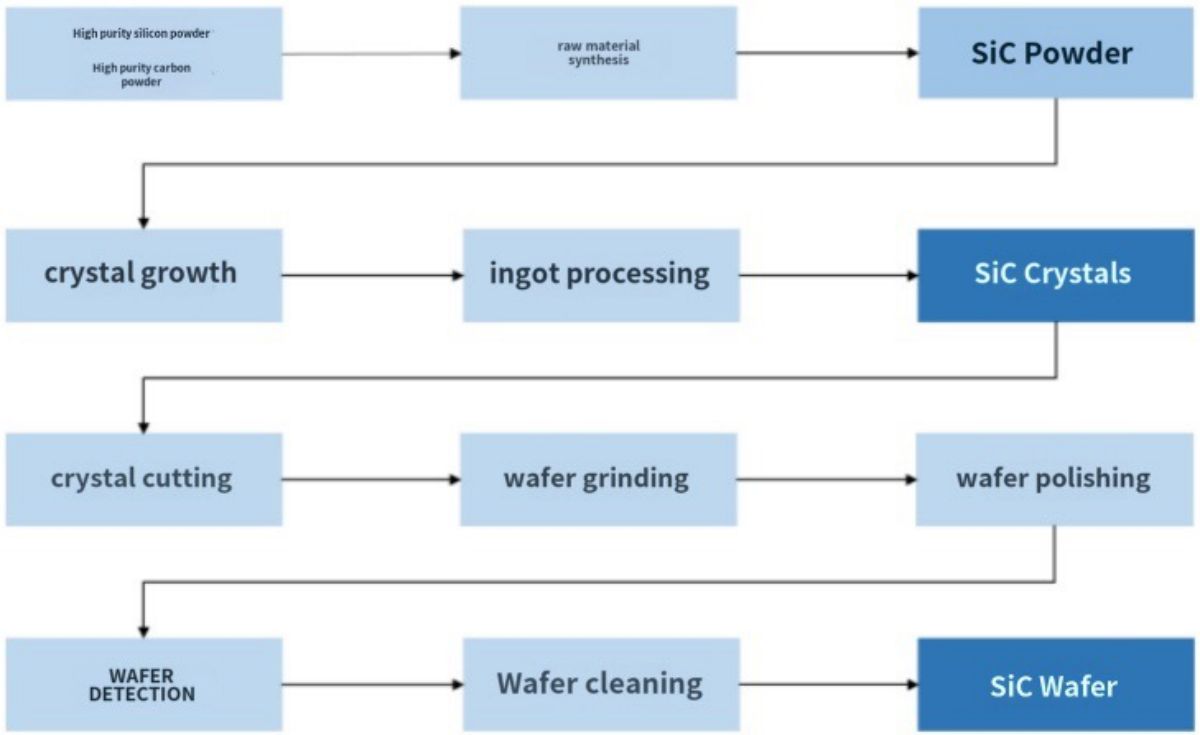
Підготовка SiC-підкладки є складною, що призводить до її високої ціни.
Контроль температурного поля є складним: для вирощування кристалічних стрижнів Si потрібно лише 1500℃, тоді як кристалічні стрижні SiC потрібно вирощувати за високої температури понад 2000℃, і існує понад 250 ізомерів SiC, але основна монокристалічна структура 4H-SiC для виробництва енергетичних пристроїв, якщо не контролювати точно, отримає інші кристалічні структури. Крім того, градієнт температури в тиглі визначає швидкість сублімаційного переносу SiC та розташування та режим росту газоподібних атомів на кристалічній поверхні розділу, що впливає на швидкість росту кристалів та їх якість, тому необхідно розробити систематичну технологію контролю температурного поля. Порівняно з кремнієвими матеріалами, різниця у виробництві SiC також полягає у високотемпературних процесах, таких як високотемпературна іонна імплантація, високотемпературне окислення, високотемпературна активація та процес твердої маски, що вимагається цими високотемпературними процесами.
Повільний ріст кристалів: швидкість росту стрижня з кристалів Si може досягати 30 ~ 150 мм/год, а виробництво стрижня з кристалів кремнію довжиною 1-3 м займає лише близько 1 дня; наприклад, стрижень з кристалів SiC, отриманий методом PVT, має швидкість росту близько 0,2-0,4 мм/год, виростає менше ніж на 3-6 см за 7 днів, швидкість росту становить менше 1% від кремнієвого матеріалу, виробничі потужності вкрай обмежені.
Високі параметри продукту та низький вихід: основні параметри підложки SiC включають щільність мікротрубочок, щільність дислокацій, питомий опір, деформацію, шорсткість поверхні тощо. Розташування атомів у закритій високотемпературній камері та повний ріст кристалів, контролюючи при цьому показники параметрів, є складною системною інженерією.
Матеріал має високу твердість, високу крихкість, тривалий час різання та високий знос: твердість SiC за шкалою Мооса 9,25 поступається лише алмазу, що призводить до значного збільшення складності різання, шліфування та полірування, і для вирізання 35-40 шматків злитка товщиною 3 см потрібно приблизно 120 годин. Крім того, через високу крихкість SiC знос при обробці пластин буде більшим, а коефіцієнт виходу становить лише близько 60%.
Тенденція розвитку: Збільшення розміру + зниження ціни
Глобальний ринок SiC для виробництва 6-дюймових об'ємних ліній виробництва переходить у стадію дозрівання, і провідні компанії вийшли на ринок 8-дюймових пластин. Вітчизняні проекти розвитку в основному спрямовані на 6-дюймові пластини. Хоча більшість вітчизняних компаній все ще базуються на 4-дюймових виробничих лініях, галузь поступово розширюється до 6-дюймових. З розвитком технології допоміжного обладнання для 6-дюймових пластин, вітчизняна технологія SiC-підкладок також поступово вдосконалюється, що відобразиться на економії від масштабу великогабаритних виробничих ліній, і поточний розрив у часі масового виробництва 6-дюймових пластин на вітчизняному ринку скоротиться до 7 років. Більший розмір пластини може призвести до збільшення кількості окремих кристалів, покращення коефіцієнта виходу продукції та зменшення частки крайових кристалів, а вартість досліджень і розробок та втрата виходу продукції залишатиметься на рівні близько 7%, тим самим покращуючи коефіцієнт використання пластин.
У проектуванні пристроїв все ще існує багато труднощів
Комерціалізація SiC-діодів поступово вдосконалюється, і наразі низка вітчизняних виробників розробили продукти SiC SBD. Продукти SiC SBD середньої та високої напруги мають хорошу стабільність, а в бортових комп'ютерах транспортних засобів використання SiC SBD+SI IGBT дозволяє досягти стабільної щільності струму. Наразі в Китаї немає перешкод для патентного дизайну продуктів SiC SBD, і розрив із зарубіжними країнами невеликий.
SiC MON все ще має багато труднощів, все ще існує розрив між SiC MON та зарубіжними виробниками, а відповідна виробнича платформа все ще перебуває в стадії розробки. Наразі ST, Infineon, Rohm та інші SiC MON на 600-1700 В досягли масового виробництва та підписали угоди та постачають їх багатьом виробничим галузям, хоча поточна вітчизняна розробка SiC MON в основному завершена, низка виробників співпрацює з фабриками на етапі виробництва пластин, а подальша перевірка клієнтами все ще потребує деякого часу, тому до масштабної комерціалізації ще далеко.
Наразі планарна структура є основним вибором, а траншейний тип широко використовується в галузі високого тиску в майбутньому. Виробників SiC MON з планарною структурою багато, планарна структура не так легко створює локальні проблеми з пробійами порівняно з пазовою, що впливає на стабільність роботи, на ринку нижче 1200 В має широкий спектр застосування, а планарна структура є відносно простою у виробництві, що відповідає двом аспектам технологічності та контролю витрат. Пазовий пристрій має переваги надзвичайно низької паразитної індуктивності, швидкої швидкості перемикання, низьких втрат та відносно високої продуктивності.
2--Новини про SiC-пластини
Зростання виробництва та продажів на ринку карбіду кремнію, зверніть увагу на структурний дисбаланс між попитом та пропозицією
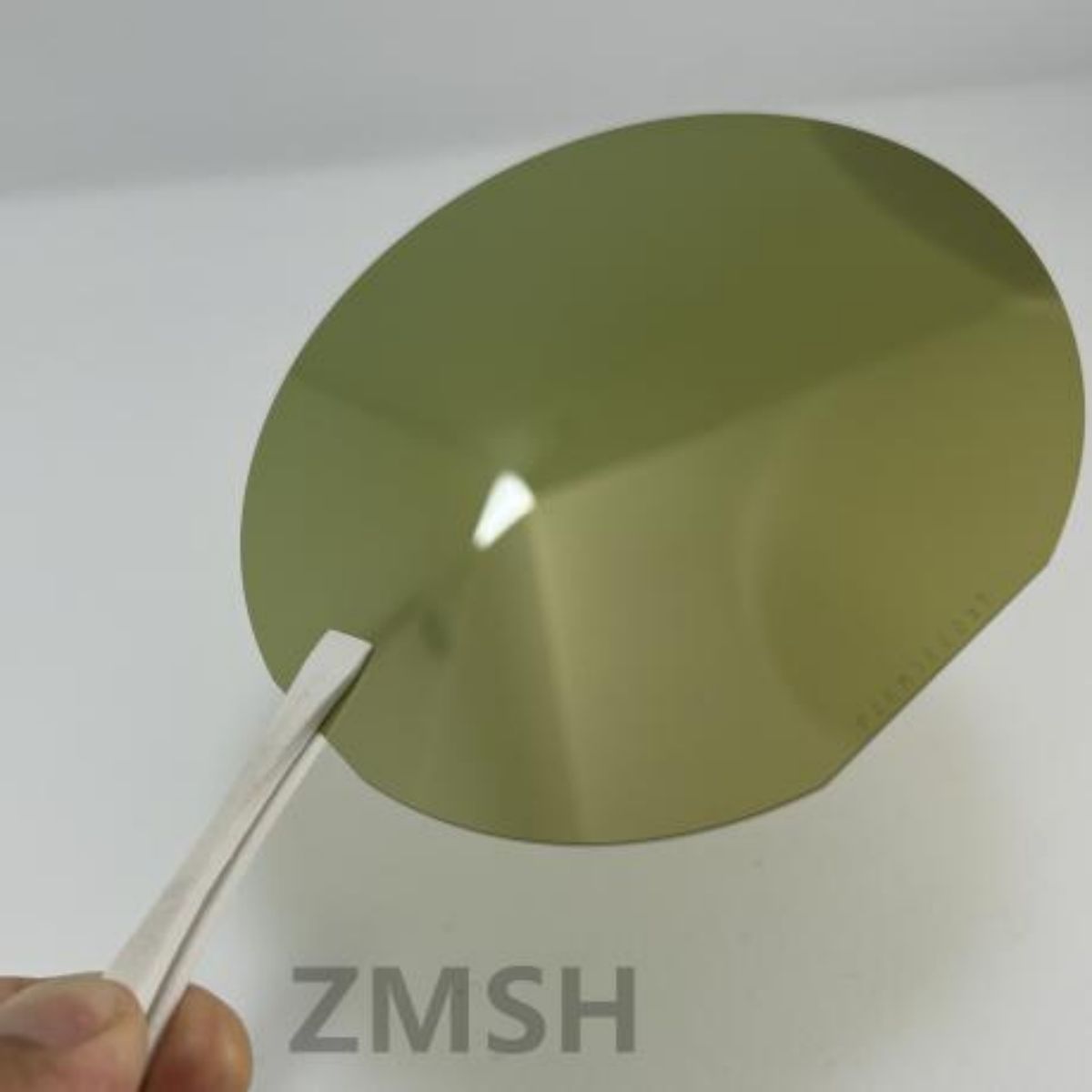
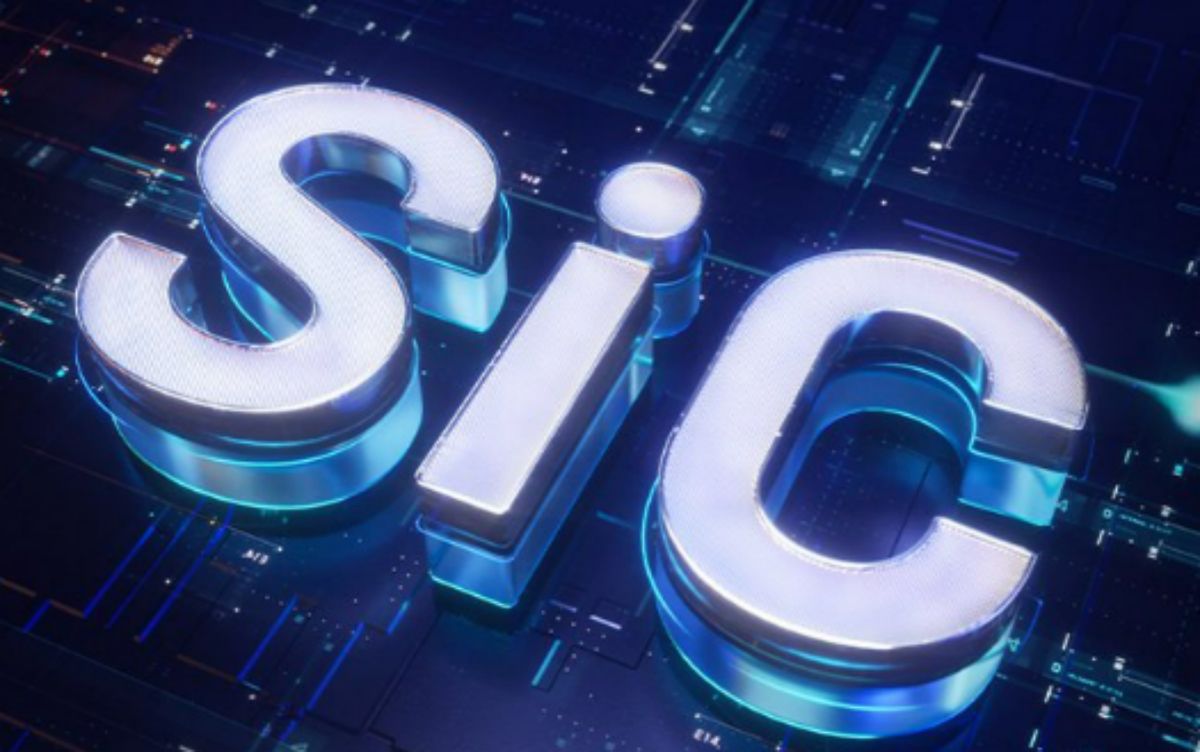
Зі швидким зростанням ринкового попиту на високочастотну та потужну силову електроніку, фізичне обмеження напівпровідникових приладів на основі кремнію поступово стало помітним, і напівпровідникові матеріали третього покоління, представлені карбідом кремнію (SiC), поступово стали промислово розвинені. З точки зору матеріальних характеристик, карбід кремнію має втричі більшу ширину забороненої зони, ніж кремнієвий матеріал, в 10 разів більшу критичну напруженість електричного поля пробою та втричі більшу теплопровідність, тому силові прилади на основі карбіду кремнію підходять для високочастотних, високотискних, високотемпературних та інших застосувань, допомагаючи підвищити ефективність та щільність потужності силових електронних систем.
Наразі на ринку поступово з'являються SiC-діоди та SiC-MOSFET, і з'являються більш зрілі продукти, серед яких SiC-діоди широко використовуються замість кремнієвих діодів у деяких галузях, оскільки вони не мають переваги зворотного відновлювального заряду; SiC-MOSFET також поступово використовується в автомобільній галузі, накопиченні енергії, зарядних батареях, фотоелектричних системах та інших галузях; у сфері автомобільних застосувань тенденція до модуляризації стає все більш помітною, для досягнення високої продуктивності SiC необхідно спиратися на передові процеси упаковки, технічно з відносно зрілою оболонковою герметизацією як основним напрямком, майбутнє або розробка пластикової герметизації, її індивідуальні характеристики більше підходять для SiC-модулів.
Швидкість падіння ціни на карбід кремнію або щось неймовірне
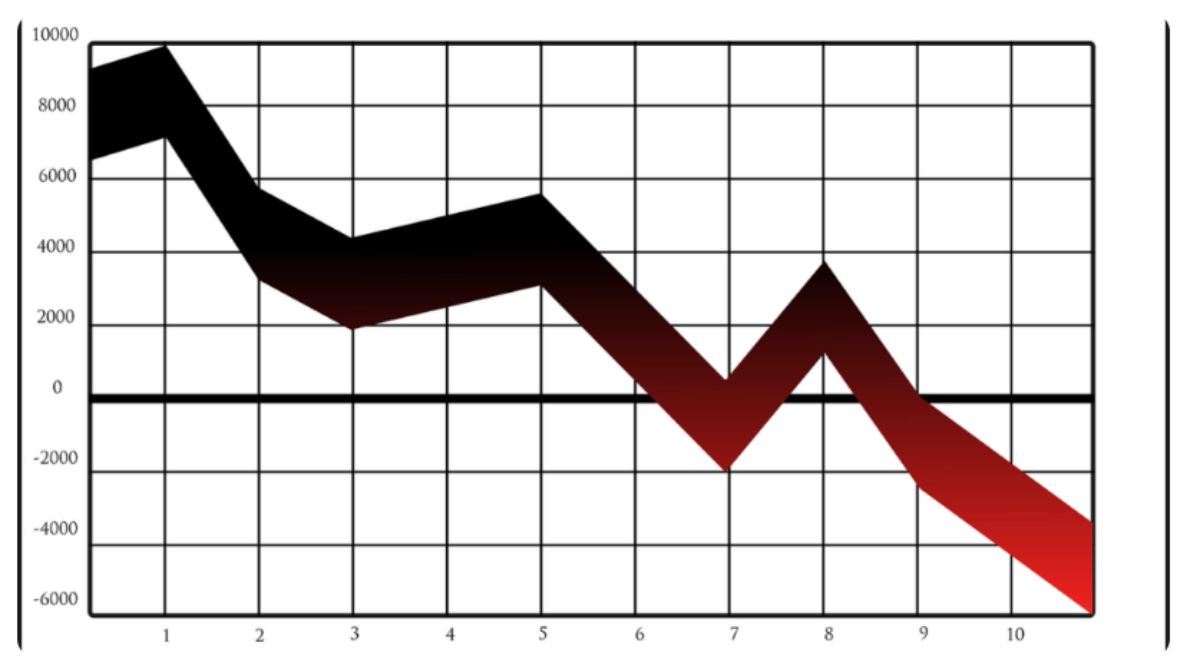
Застосування пристроїв на основі карбіду кремнію головним чином обмежується високою вартістю. Ціна SiC MOSFET на тому ж рівні в 4 рази вища, ніж у Si IGBT. Це пояснюється складністю процесу виробництва карбіду кремнію, в якому ріст монокристалів та епітаксія не тільки негативно впливають на навколишнє середовище, але й темпи росту повільні, а обробка монокристалів у підкладку повинна проходити процес різання та полірування. Через особливості матеріалу та незрілу технологію обробки вихід вітчизняної підкладки становить менше 50%, а різні фактори призводять до високої вартості підкладки та епітаксії.
Однак, структура витрат на пристрої з карбіду кремнію та пристрої на основі кремнію є діаметрально протилежною: витрати на підкладку та епітаксіальну обробку переднього каналу становлять відповідно 47% та 23% від вартості всього пристрою, що загалом становить близько 70%, витрати на проектування, виготовлення та герметизацію пристрою заднього каналу становлять лише 30%, вартість виробництва пристроїв на основі кремнію в основному зосереджена на виробництві пластин заднього каналу близько 50%, а вартість підкладки становить лише 7%. Явище перевернутого ланцюга вартості промисловості карбіду кремнію означає, що виробники епітаксіальної обробки підкладок мають основне право говорити, що є ключем до структури вітчизняних та іноземних підприємств.
З динамічної точки зору ринку, зниження вартості карбіду кремнію, окрім покращення процесу виготовлення довгих кристалів та нарізки карбіду кремнію, призводить до розширення розміру пластини, що також є зрілим шляхом розвитку напівпровідників у минулому. Дані Wolfspeed показують, що збільшення розміру підкладки з карбіду кремнію з 6 дюймів до 8 дюймів може збільшити виробництво кваліфікованих мікросхем на 80%-90%, що допоможе покращити вихід продукції. Це може знизити загальну собівартість одиниці продукції на 50%.
2023 рік відомий як «перший рік 8-дюймового карбіду кремнію». Цього року вітчизняні та іноземні виробники карбіду кремнію прискорюють розробку 8-дюймових карбідних підкладок, наприклад, Wolfspeed інвестувала 14,55 мільярда доларів США у розширення виробництва карбіду кремнію, важливою частиною чого є будівництво заводу з виробництва 8-дюймових карбідних підкладок. Щоб забезпечити майбутні постачання 200-міліметрового голого металу карбіду кремнію низці компаній, Domestic Tianyue Advanced та Tianke Heda також підписали довгострокові угоди з Infineon на постачання 8-дюймових карбідних підкладок у майбутньому.
Починаючи з цього року, карбід кремнію збільшиться з 6 до 8 дюймів. Wolfspeed очікує, що до 2024 року вартість одиниці мікросхеми 8-дюймової підкладки порівняно з вартістю одиниці мікросхеми 6 дюймів у 2022 році знизиться більш ніж на 60%, а зниження вартості ще більше відкриє ринок застосувань, зазначають дослідницькі дані Ji Bond Consulting. Поточна частка ринку 8-дюймових продуктів становить менше 2%, і очікується, що до 2026 року вона зросте приблизно до 15%.
Фактично, темпи зниження ціни на карбід-кремнієві підкладки можуть перевершити уяву багатьох людей. Поточна ринкова пропозиція 6-дюймових підкладок становить 4000-5000 юанів/шт. Порівняно з початком року вона значно впала, і очікується, що наступного року вона впаде нижче 4000 юанів. Варто зазначити, що деякі виробники, щоб першими вийти на ринок, знизили ціну продажу до рівня собівартості. Це відкрило модель цінової війни, яка в основному зосереджена на постачанні карбід-кремнієвих підкладок у сфері низької напруги. Вітчизняні та іноземні виробники агресивно розширюють виробничі потужності або ж раніше, ніж очікувалося, допускають перевищення пропозиції карбід-кремнієвих підкладок.
Час публікації: 19 січня 2024 р.